Meet Blair
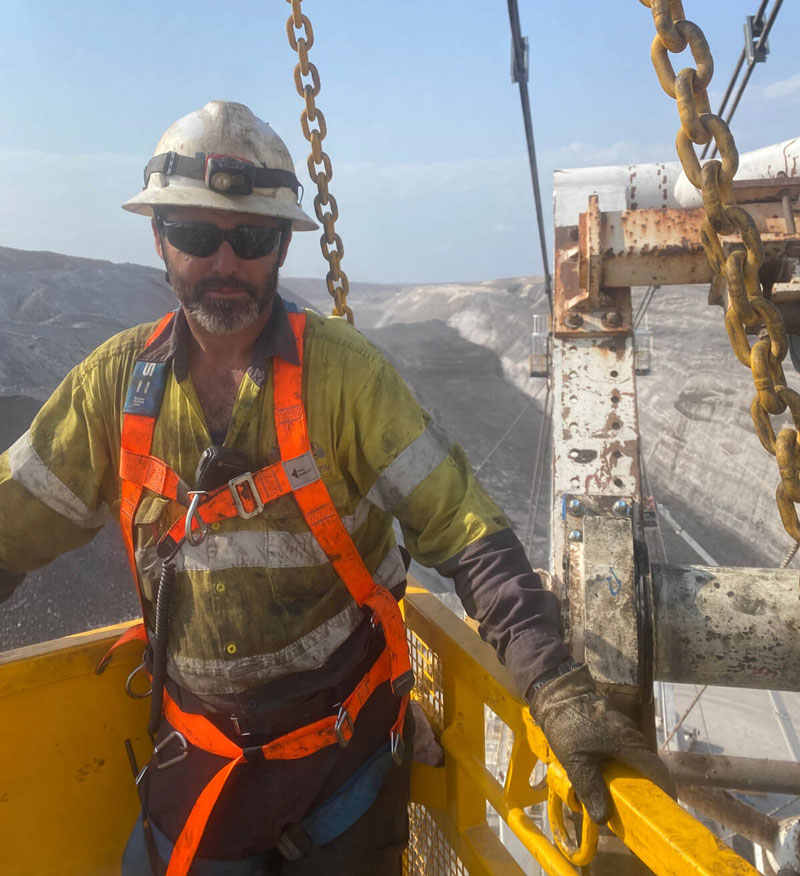
I left my Job as a contract Carpenter in the Brisbane region in Dec 2011 and started with Downer EDI Mining at Goonyella at an entry level position as a Workshop Serviceman. A Workshop Serviceman cleans and services a wide variety of equipment, changing fluids and filters and carrying out thorough checklists to find any defects present.
Even though this was an entry level position, it paid much more than my hardworking carpentry work and mining was much more of a secure income over contract work as it was always pending on the weather and availability of material etc. Mining was ideal for my family (my wife Laetitia and son Hunter). Serviceman work suited me as I very much enjoy working with my hands and I was learning all about maintaining earthmoving equipment more and more every shift. And who doesn’t love earth moving gear! My well-paid job also included keep and the camp food was pretty good too (2nds or if you could 3rds was always available). I worked at Goonyella for 2 years on an even time roster. I wasn’t used to all the time off with an even time roster, but I happily got used to it very quickly.
Moving on from Goonyella, I transferred to Meandu Mine where my wife’s parents (Wayne & Chrys) also worked and lived nearby in Kingaroy. Downer at Meandu Mine also employed me as a Serviceman, however this time I was driving a service truck refuelling equipment in the field. This was also an enjoyable job and a quick way to meet a lot of friendly operators working on my shift. My family (Laetitia, Hunter and now Scarlett) packed up our belongings and relocated to Kingaroy. This meant I was home with my family after every shift.
After 2 years of working the service truck I took a days only job working across 2 crews (still even time roster). I was to be a TA to Fitters in the workshop and occasionally in the field, also filling in for service truck operators when they were absent. The variety was great! And I was learning even more helping the Fitters where I could. The even time roster allowed for lots of family getaways and time together, even though once the locals worked out I had previous building skills, I am regularly put to work during my down time. But I am happy to do this to maintain previous skills and with the variety of work, and a busy happily settled family in Kingaroy, life was/is never boring.
Meandu Mine has a state-of-the-art workshop which is a pleasure to work in. However, as time went on I spent more and more time in the field working on diggers and drills and occasionally the dragline. All my supervisors over the years in the field and workshop were very kind to me and would often place me on good jobs where I was able to continue to learn, and the men on the floor were also very kind in sharing their knowledge.
In April 2020 the field superintendent offered me a diesel fitting apprenticeship, I was very much ready and I didn’t hesitate to accept. I was really taken under the wing of many mentors and the learning continued more in depth. In January 2024 I completed my diesel fitting apprenticeship and I continue to work in the field. I thoroughly enjoy my job and I look forward to continuing my career and continuing to grow when the opportunities present.
Over the past 12 years I have been given lots of training including:
Brake testing, forklifts, franna and gantry cranes, dogging skills, confined space, working at heights, parker training in making hoses, hastings training in pumps and SOS sampling, fire suppression training, move and test pass outs on most onsite equipment, training in operating skid steers and loaders, hydraulic flow testing, driving rigid trucks, towing large trailers and restraining loads the list goes on, I have been very well looked after.
Why did you decide to join BUMA and what motivated you to continue to pursue a career?
BUMA offers a well-paid, safe job with the security to support my family.
What specific skills or knowledge have you gained during your apprenticeship?
I have gained many mechanical skills in the art of maintaining earthmoving equipment across site, shared by many kind Fitters and from studying books and of course from making mistakes.
Can you share a challenging task or project that helped you develop new skills?
Being appointed and trusted to be a break down fitter is at times a challenging task and a fast way to develop, as no one wants to be responsible for down time.
How has the on-the-job training contributed to your professional development?
On the job training is my preferred training method as I am a simple lad, “monkey see, monkey do.” As well as there is a strong support network onsite, seems nobody wants to see a fellow worker fail, yet build you up to be a professional.
Can you describe a hands-on experience that was particularly impactful for your learning?
It is hard to single out one experience that I was most impacted by as most days I am impacted by something new or different as there is such a broad work scope. If I was to choose one, I was placed to work with a boiler maker who was also early in his career to replace the upper hoist rope sheeves out of a man basket, hanging off a hook of a 80T crane with its fly jib attached. We successfully completed the task and was pretty chuffed with our achievements as not only did we have to change out the sheeves but to keep our cool whilst directing two cranes, one 140T to support and remove the sheeves but the other 80T crane to position our man basket where we needed to be (photos attached). It was a challenging task in a controlled high-risk environment, topped with Queensland’s weather elements that really makes you feel alive. This task required thorough planning and the foresight to identify associated obstacles / hazards, the ability to work under pressure and remain calm in a high-risk situation and maintain focus whilst co-ordinating large cranes. This hands-on experience has impacted my learning by giving me the confidence to take on a task of this calibre.
What challenges have you encountered in your role, and how did you go about solving them?
In break down situations, I am often faced with challenging encounters and it’s easy to get flustered especially when there is a line of trucks lined up at a digger face waiting for you to get their digger up and running. I try to remain calm and do my best to diagnose and rectify the fault, in failing that, I refer to the manuals or OEM support or seek guidance from a veteran fitter or auto electrician who has been faced with the fault previously who will be more than happy to share some ideas. I’ve learnt it doesn’t have to be stressful and I don’t need to feel like a failure myself, some faults will just take time to go through a process of elimination until the cause is found. The quicker I came to terms with that the quicker I can get to the cause of a fault.
How do you contribute to your team, and can you share a successful collaboration experience?
Hmm… this might be better answered by a team member of mine to what he thinks I bring to the team. Without sounding like I am blowing my own trumpet, I think I bring a positive can do attitude and plenty of momentum. No one likes a work mate that avoids work while you are working hard to get through the planned tasks for the day or get a machine up and running. You know, like a “sensor light” (only works when someone walks past) or “the cane toad” (he sits down every time he stops).
How would you describe the company culture?
I can only comment on my opinion of the company culture at Meandu. Meandu has a lot of strong friendships and the vibe is mostly always friendly. Alot of the people have been working at the mine for many years which is a testament to the workplace. There is always a few who may have been there a little long to forget how good they have it or are possibly in need of change. But overall, I would say it’s healthy with room to improve.
In what ways do you see your role evolving within the company or in the industry?
I have plenty of work to do yet to become a guru in my field, after that I would like to try my hand at a leading hand position and building some management skills.
Have you had a mentor during your apprenticeship, and how has that relationship impacted your learning?
I have had many mentors, some more patient and good at explaining than others. I have been very fortunate to have had so many mentors as I have been able to take away clever tricks of the trade and a better understanding from each and everyone.
How important do you think mentorship is for someone in your position?
A good mentor who is willing to take the time to answer your questions and share knowledge and take you under their wing is the difference between being a good tradesman or not. I could not rely on learning this on my own from experiences and books, I learn much better from monkey see, monkey do.
If you could offer advice to future apprentices joining the company, what would it be based on your experience?
Try not to justify your existence in the team by being a “know it all” – that’s a fast way to lose the respect of your mentors and as a result, most likely you won’t receiving the support you need. Show your keen and interested, and always be there to assist, doing your best to think ahead. This will earn respect from your mentors and most likely result in them wanting to build you up more.
Also, when you get the feeling to avoid a task because you don’t have the confidence to do it or it looks too challenging, you need to push through that uncertainty and give it a go. Even if you feel silly not knowing how to do it or having to ask for help. That way, next time you are presented with that task you’ll have built the confidence to tackle it.